Почему на ТМК нельзя пройти с шариковой ручкой?
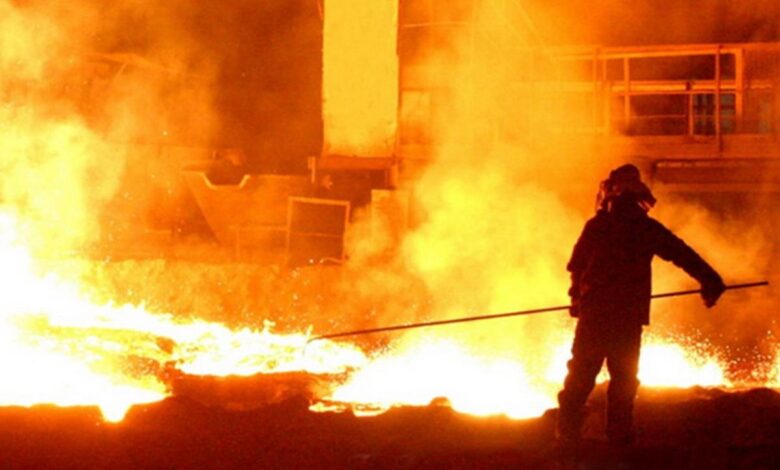
Попасть на Усть-Каменогорский титано-магниевый комбинат – настоящая удача. И она сегодня выпала мне. По приглашению ТМК я попал в сердце производства высококачественного титана для мировой аэрокосмической отрасли – в цеха комбината. Здесь, у нас – в Восточном Казахстане, в Усть-Каменогорске – производят самый прочный металл в мире, и мы сможем увидеть этот уникальный процесс.
Первым делом – безопасность
Первое, что мы со съемочной группой узнали о комбинате, – это очень серьёзное отношение к безопасности. Территория закрытая, со строгими регламентами допуска. Ну это понятно, но почему нам нельзя приносить с собой даже шариковые ручки? Подержу интригу и расскажу об этом чуть позже.
Пока же меня берёт под своё крыло Азамат Ергасымов — инженер производственно-технического управления. Сегодня он не просто высококлассный специалист комбината, но и экскурсовод. И со своей задачей справляется просто блестяще — так рассказал о сложных технологических процессах, что даже мне, человеку без специального образования, всё стало понятно. Ну, или почти всё…
Цех №12: от сырья до титанового шлака
Первый пункт моего производственного тура — цех №12. Здесь все начинается: из ильменитовой руды выплавляется титановый шлак. Цех поражает с первого взгляда! Как передать масштабный и зрелищный процесс производства титана? Спасибо, что есть не только слова, но и фото с видео. Иначе бы, честное слово, не справился.
В огромной, высотой с девятиэтажный дом, рудно-термической печи идет плавка. Специалисты управляют технологическим процессом через автоматизированную систему управления, задают нужные параметры плавки, контролируют его через почти 300 датчиков. «Разгоняется» печь до температуры 1 800 градусов. А дальше происходит чудо, свидетелем которого я стал, – течет самая настоящая огненная река, а металлурги «подгоняют» её специальными инструментами, которые называются трамбовки. Каждый удар – эффектный всполох сверкающих брызг титанового шлака!
«Это самый первый передел в процессе производства нашего основного товарного продукта – титана», — поясняет Азамат Ергасымов.
Цех №1: ванна для магния
Наш сопровождающий ведёт меня в следующий цех. Для получения титановой губки используется магний, и в цехе №1 жидкий хлорид магния разделяют на газ (хлор) и металл (магний).
Для этого в цехе установлены огромные ванны, в которых, конечно же, никто не купается. Они вообще ничем не похожи на привычные домашние ванны, кроме названия.
— Видите на поверхности поблескивание? Это и есть магний — показывает Азамат на кипящий, бурлящий электролит.
Цех – огромный, и за его работой мастер смены и оператор наблюдают в щитовой. Здесь на экраны выведены все параметры – температура, уровень расплава, напряжение. Весь процесс автоматизирован, производство ведётся непрерывно.
Цех №3: из огня да в холодильник
Титановая губка, добытая из руды – это сырье для слитков и сплавов. А рождается она в цехе №3. Сформированный блок губчатого титана, поры которого заполнены примесями магния и хлорида магния, необходимо полностью очистить от этих примесей. Для этого огромный аппарат нагревают до 1 000 градусов, в вакууме очищают титан от примесей и затем помещают в холодильник для охлаждения.
— После окончания процесса охлаждения, титан губчатый передается на следующий передел для его переработки в товарную продукцию.
Цех №14: кухня космических стандартов
Обычно именно сюда приводят высоких гостей, чтобы показать им и готовую продукцию, и красивый, современный процесс вакуумно-дуговой плавки. Цех похож на гигантскую суперсовременную кухню со сложным оборудованием.
Для каждого сплава есть своя рецептура. А основной ингредиент – кусочки титановой губки, произведенной в цехе №3, в котором я уже побывал. Их перемешивают с легирующими компонентами и микродобавками и отправляют в пресс, чтобы сформировать половинки «бублика». Из них потом с помощью плазменной сварки получается гигантский титановый цилиндр. Через специальные смотровые окна я вижу, как зеленоватые «молнии» соединяют вместе металлические части.
После сварки цилиндр, ставший единым целым, отправляется на основной переплав в вакуумно-дуговую печь. Это главное, что должно произойти с титаном, чтобы из него можно было делать детали самолётов или айфонов. Мой великолепный экскурсовод говорит, что закуп этих печей фактически дал новое дыхание УК ТМК в 2010-м году, позволив выпускать слитки и сплавы. Причем, такого качества, что они сертифицированы на соответствие требованиям аэрокосмического стандарта AS 9100.
Что не так с шариковой ручкой?
И, наконец, о шариковой ручке. В шарике на конце стержня содержится тугоплавкий вольфрам. Его температура плавления выше, чем у титана (3422 С против 1668 С). Если такой шарик случайно попадёт в сырьё – он не расплавится ни в кипящем электролите, ни при плазменной сварке, ни в вакуумно-дуговой печи. Изделие с нерасплавленным вкраплением может не выдержать нагрузок и треснуть. А теперь представьте, если это будет запчасть самолёта?
И поэтому безопасность и качество продукции на комбинате превыше всего. Поэтому шариковым ручкам на ТМК не оставляют шансов даже в кабинетах. Офисные работники используют исключительно линеры. Мелочь? Да, но она – символ того, что на комбинате уделяют максимум внимания даже шарику размером с миллиметр. Итог такого отношения – производство высококачественного титана, который помогает людям не только отправляться в космос, но и делать шаг за пределы возможного в других сферах!
Semeynews.kz